WEl – P1 Product info
WEL – P1
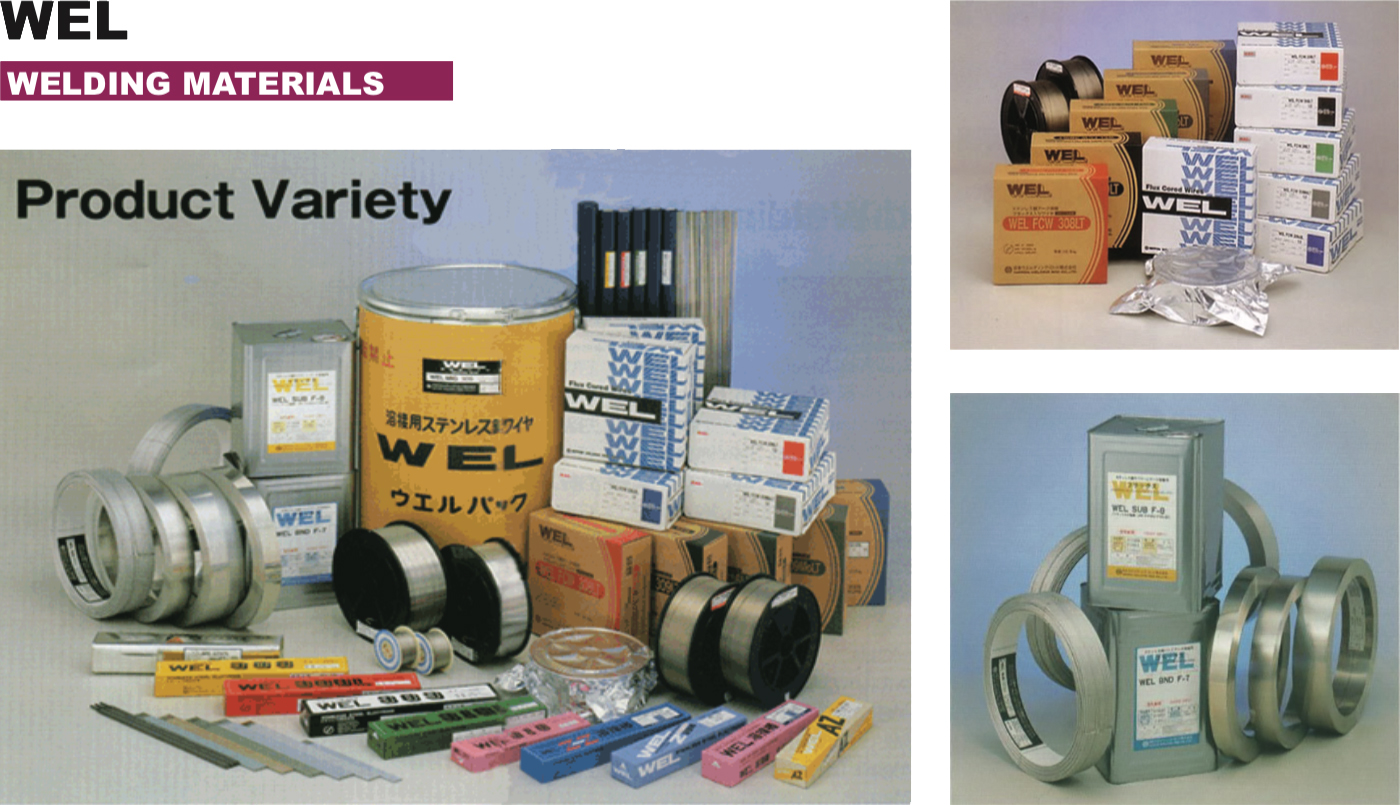
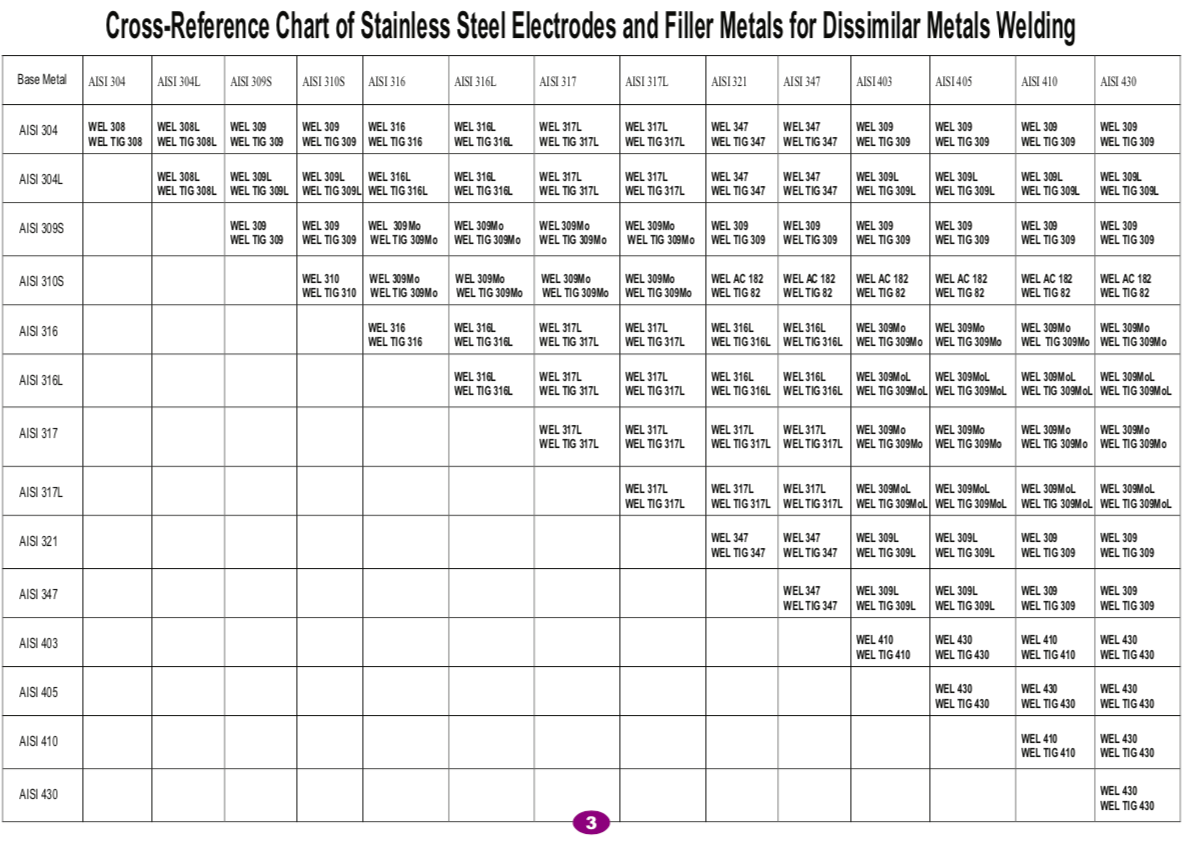
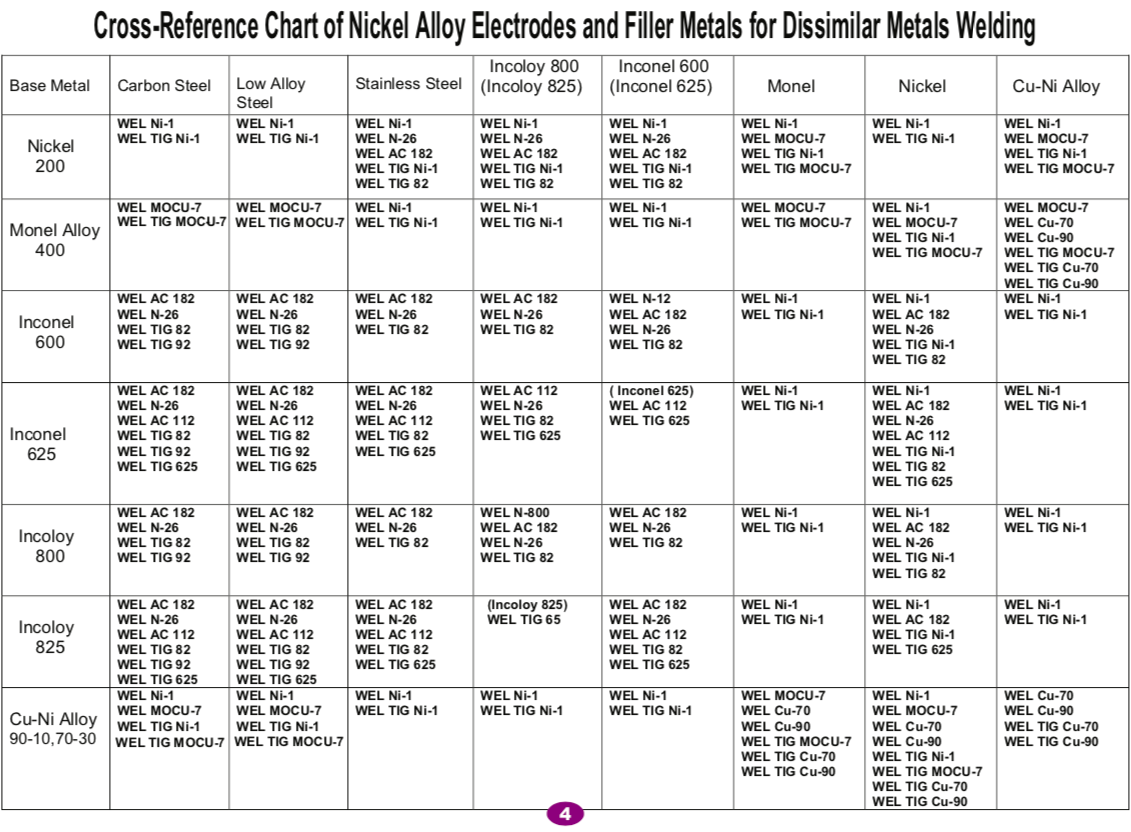
WEL Covered Welding Electrodes
The weldability of covered welding electrode can be changed with the type of the covering.It must be suitably selected the type of the covering of covered welding electrode for the purpose of welding operations, and adequate selection reveals good efficiency resulting economical performance to welding.
Other than the ordinary type of the covering, CLEAN “Z’’ type electrode and “AZ’’ type electrode are prepared for the purpose of welding operation.
Characteristics of WEL Covered Welding Electrode
- WEL Type of Covering …………..Good weldability with sound weldment
- CLEAN “Z’’ Type of Covering ….. Less spatter and good slag removability
- “AZ’’ Type of Covering …………..Excellent beautiful bead appearance, especially flatbead gained at vertical and overhead positions.
WEL Covered Welding Electrodes for Cast Iron
There are mainly four (4) kinds of covered welding electrode for cast iron used core wire of carbon steel, cast iron, copper alloy and nickel alloy. In our electrode, special type of coverings are covered on nickel alloy core wire such as pure nickel, Ferous-Nickel and Monel metal so that it is very easy to perform welding without pre-heating the base metal.
These types of electrode are very easy for welding operation and they are also easy to perform machining of weldment for reduction of heat affection to cast iron.
Why welding of cast iron is not so easy.
Difficulty of arc welding to cast iron is dependent upon the following reasons :
1) Carbon content in cast iron is very high.
2) Weld metal can be hardened by transfer the carbon in heat-affected zone to weld metal.
3) Heat-affected zone in cast iron will be chilled with high speed heating and cooling and then
it will be severely hardened.
4) For prevention to above condition, it is necessary to establish such a large pre-heat and
post-heat equipment.
Good availability for welding of cast iron. It is the best method to perform welding of cast iron by use of electrode which produced with nickel alloy core wire for performance of easy welding. The followings are considered as the reason why,
1) The carbon in heat-affected zone in cast iron will not be transfer into weld metal so that weld metal does not show remarkable high hardness.
2) Heat input into cast iron is lower because of the low melting point of core wire so that heat-affected zone in cast iron is maintained sound properties.
3) The cracking in bead and heat-affected zone can be prevented by peening operation.
4) It can be gained sound and machinable weldment without pre-heating and post-heating
operation.